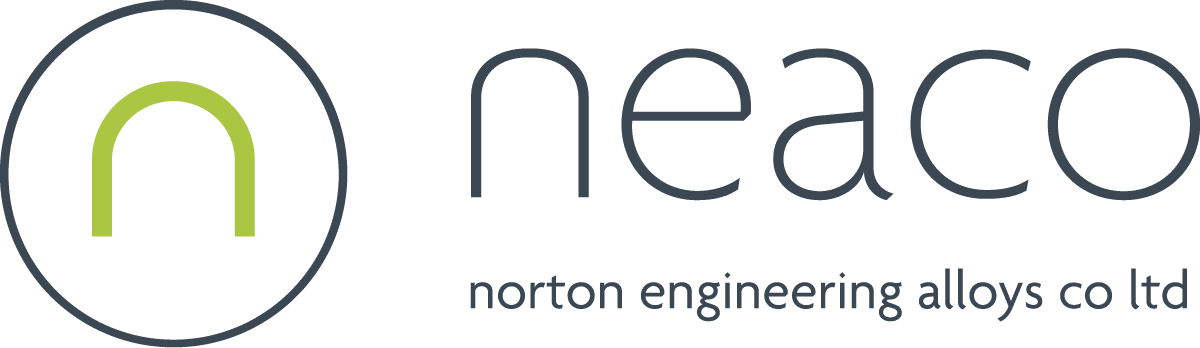
Dan Verity, the factory manager, took the students on an extensive tour of the factory. The tour included a demonstration of our swage press machine.
All the students got so much from it and the bus journey back was fantastic - they were so enthused by everything they saw and they fired dozens of questions at me about engineering and career opportunities.”
Mr Andy Grayshan | Head of the Technology and Engineering Department
During this tour, Verity explained the importance of apprenticeships in the engineering field and how hands-on experience could help them with their career paths. He guided the students through the production process at Neaco, beginning in the flooring department where Neaco manufactures its modular aluminium flooring.
The aluminium flooring is being punched by the Denley multi-punch machine.
The flooring is being fed through the 150-tonne swage press machine creating our patent swage lock design on the flooring that makes it have superior strength.
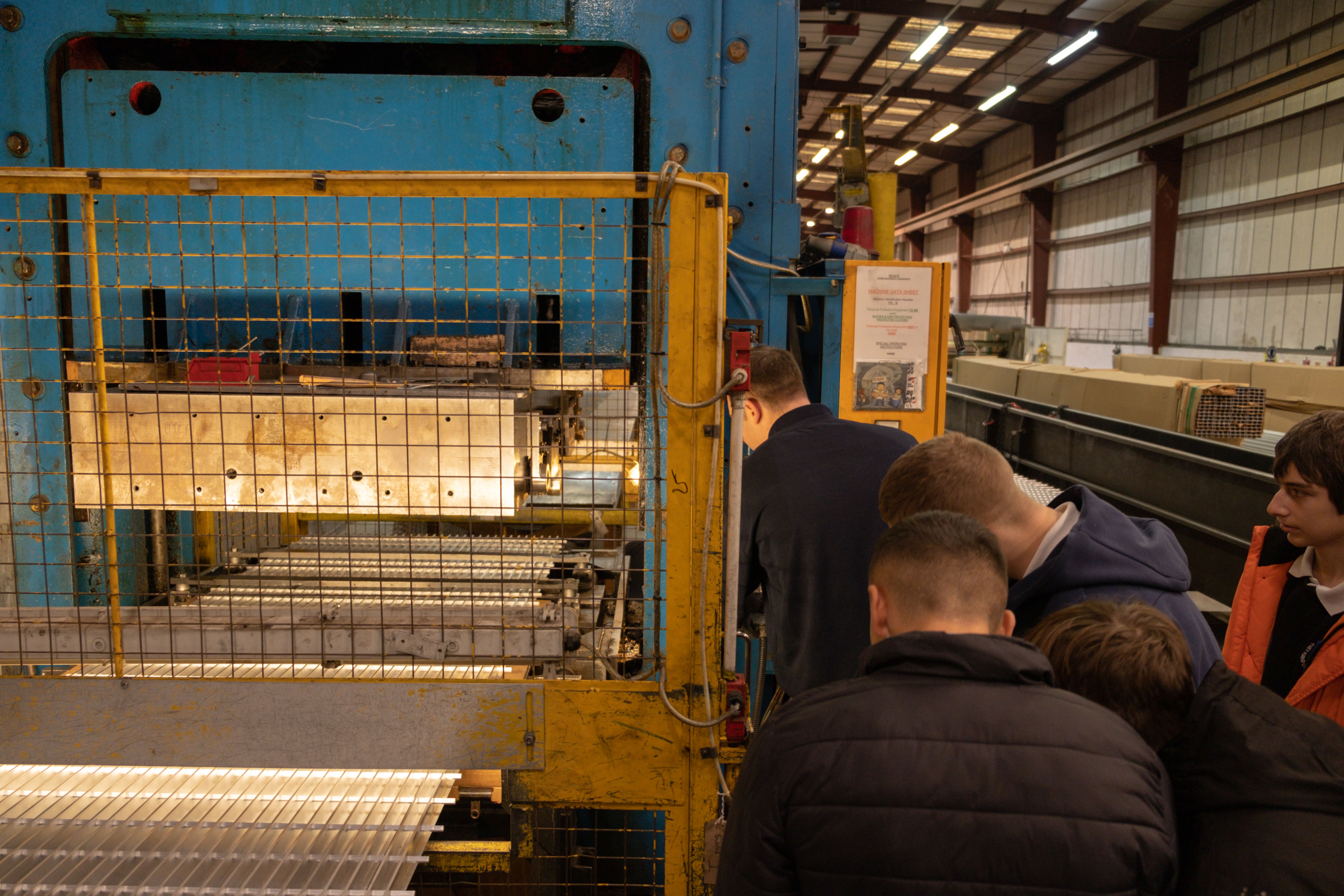
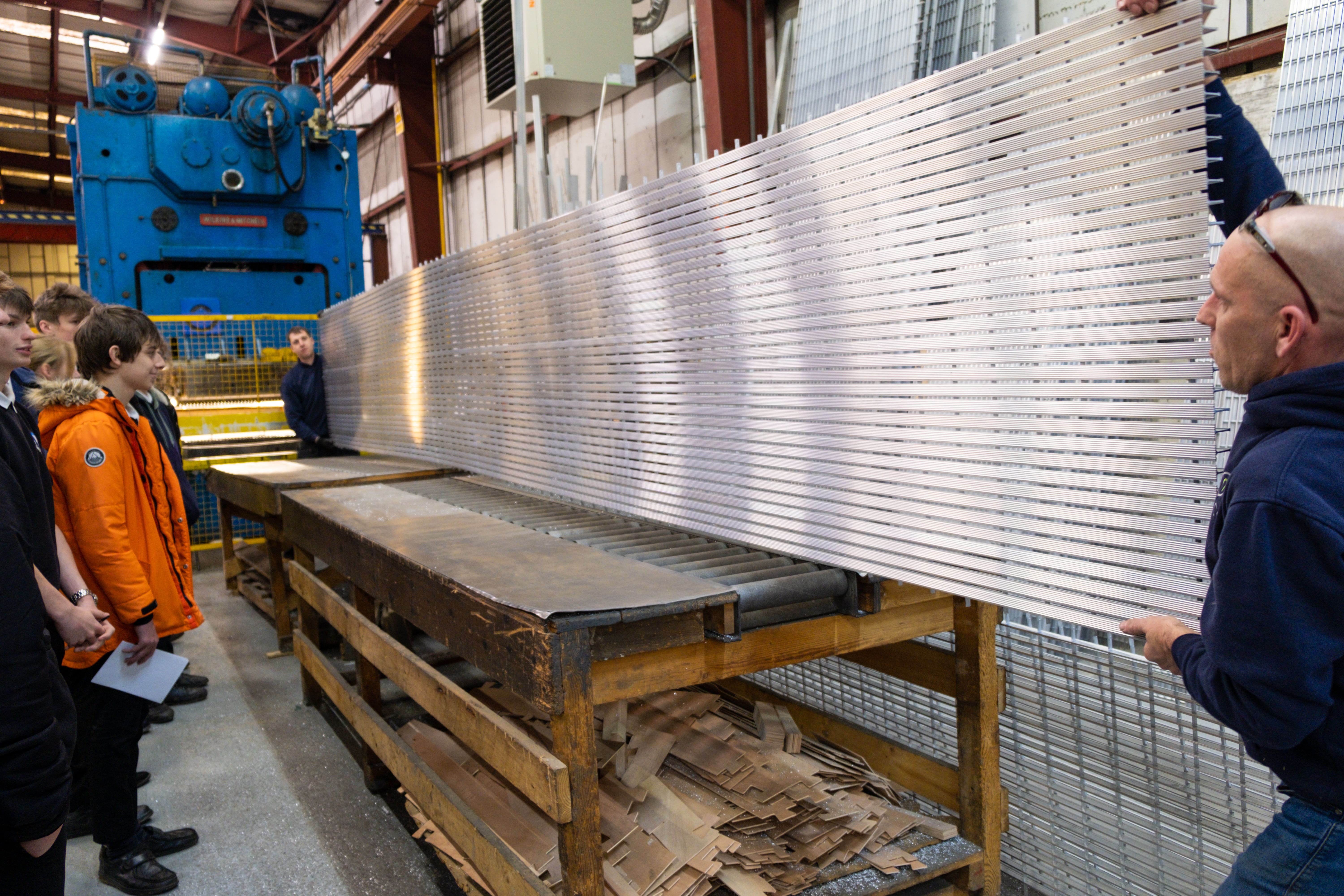
The CAD drawings of the projects are studied by all our Neaco engineers before the flooring is cut to shape with the cross-cut saw to ensure precision.
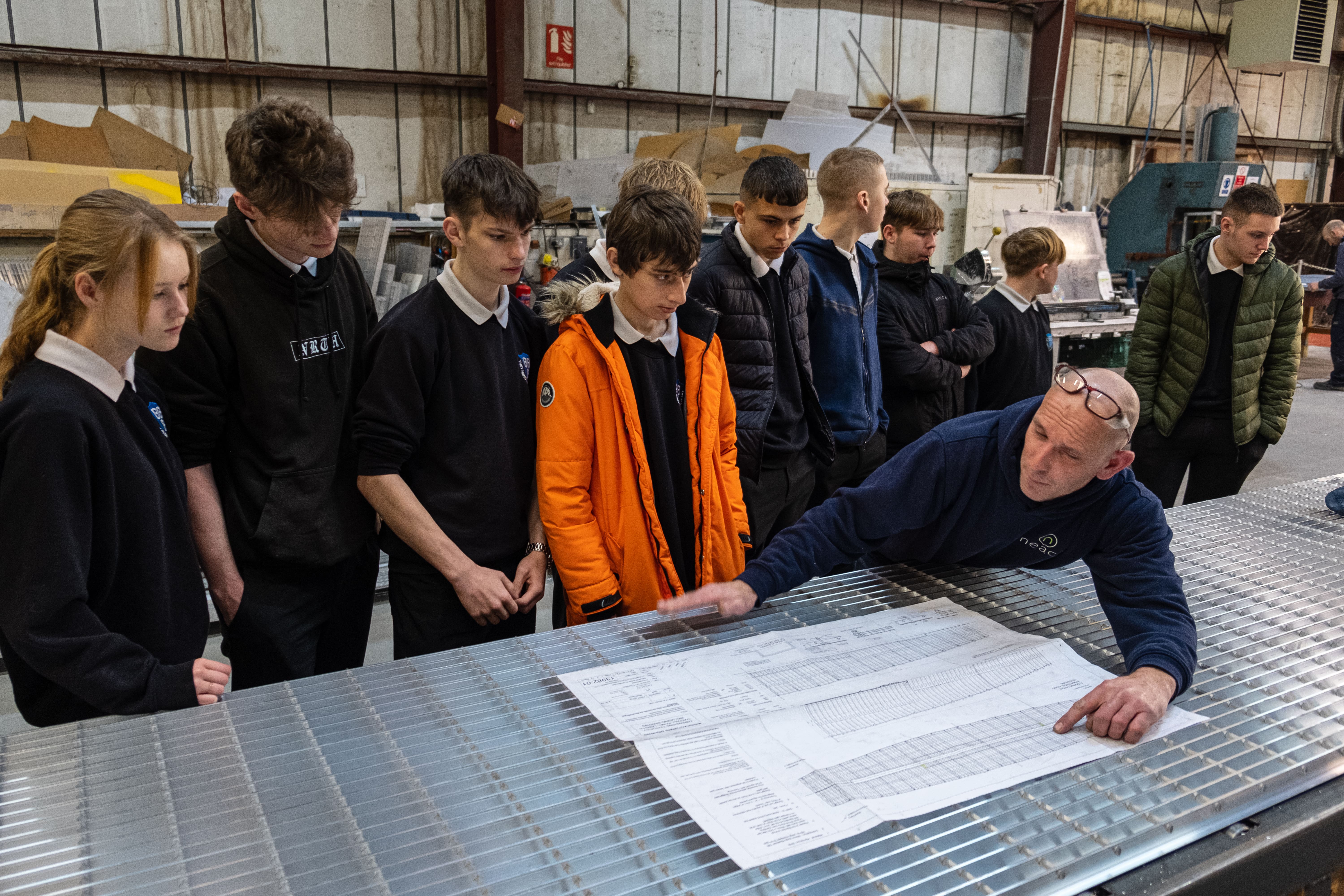
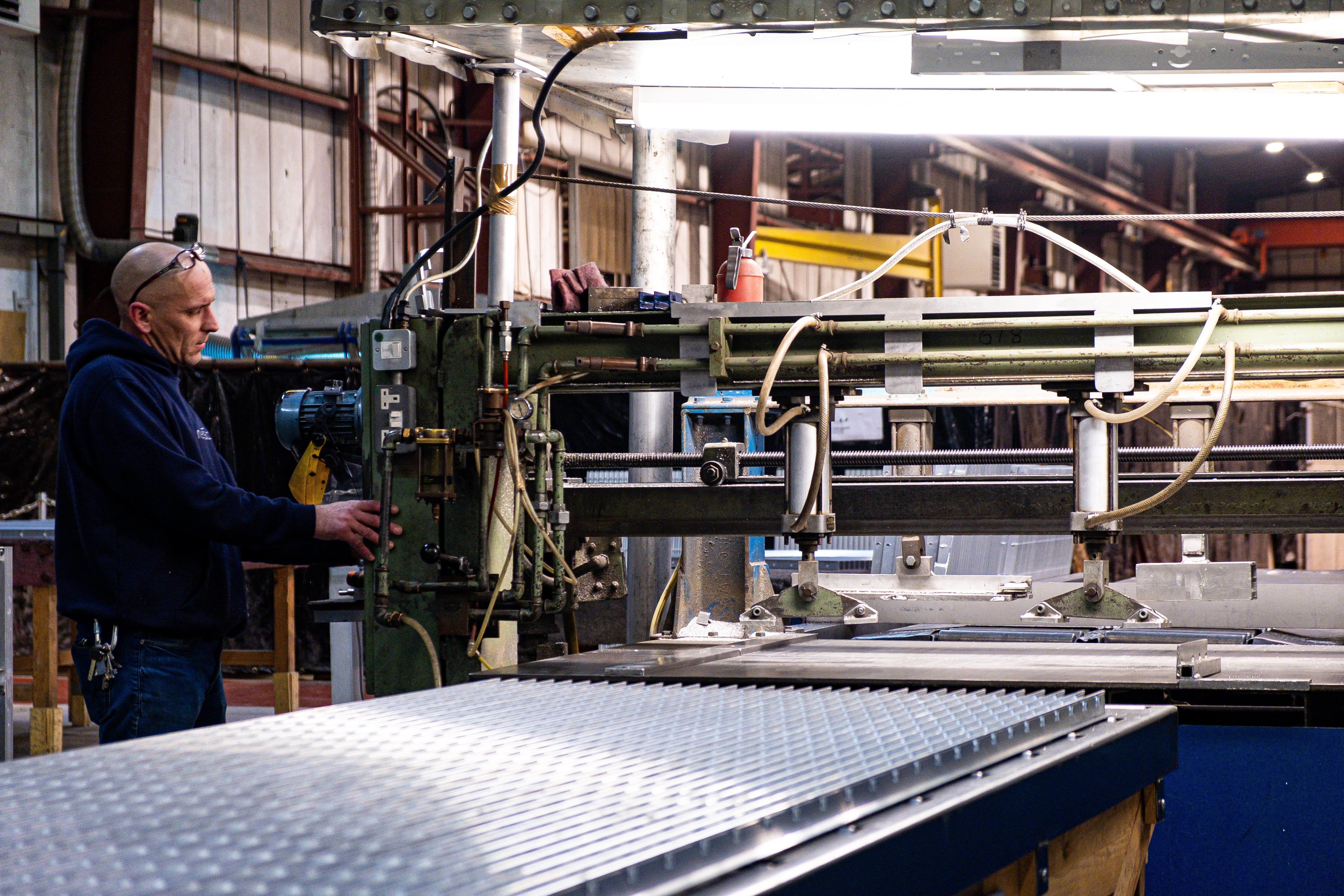
Ultimately, the students witnessed first-hand the whole process including all the inspection checks before our products are moved into the packing department.
Verity then took the students to the fabrication department where the balustrade is manufactured. They experienced two demonstrations of the Mewag hydraulic man drill bending machines, including the health and safety of using the different machinery.
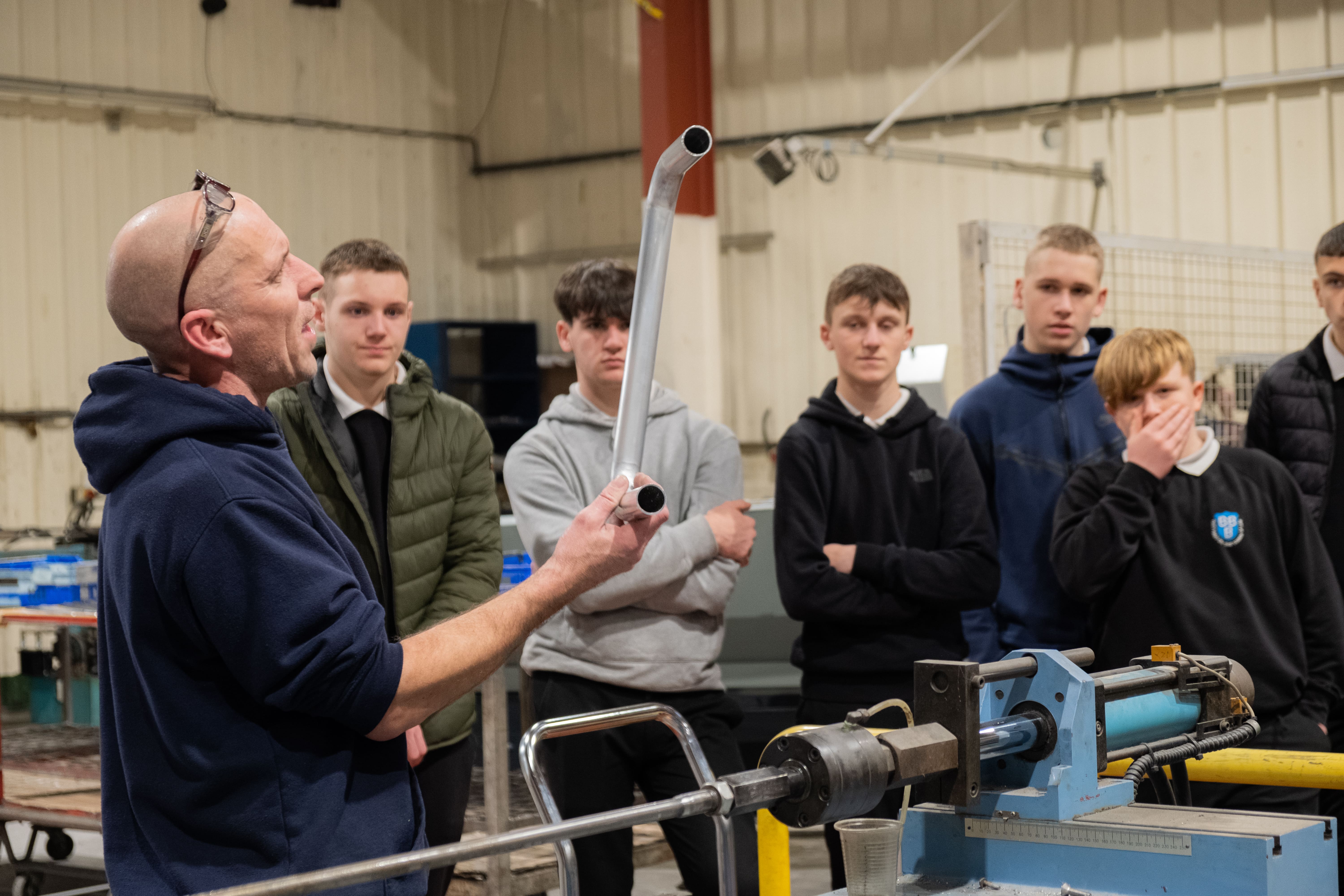
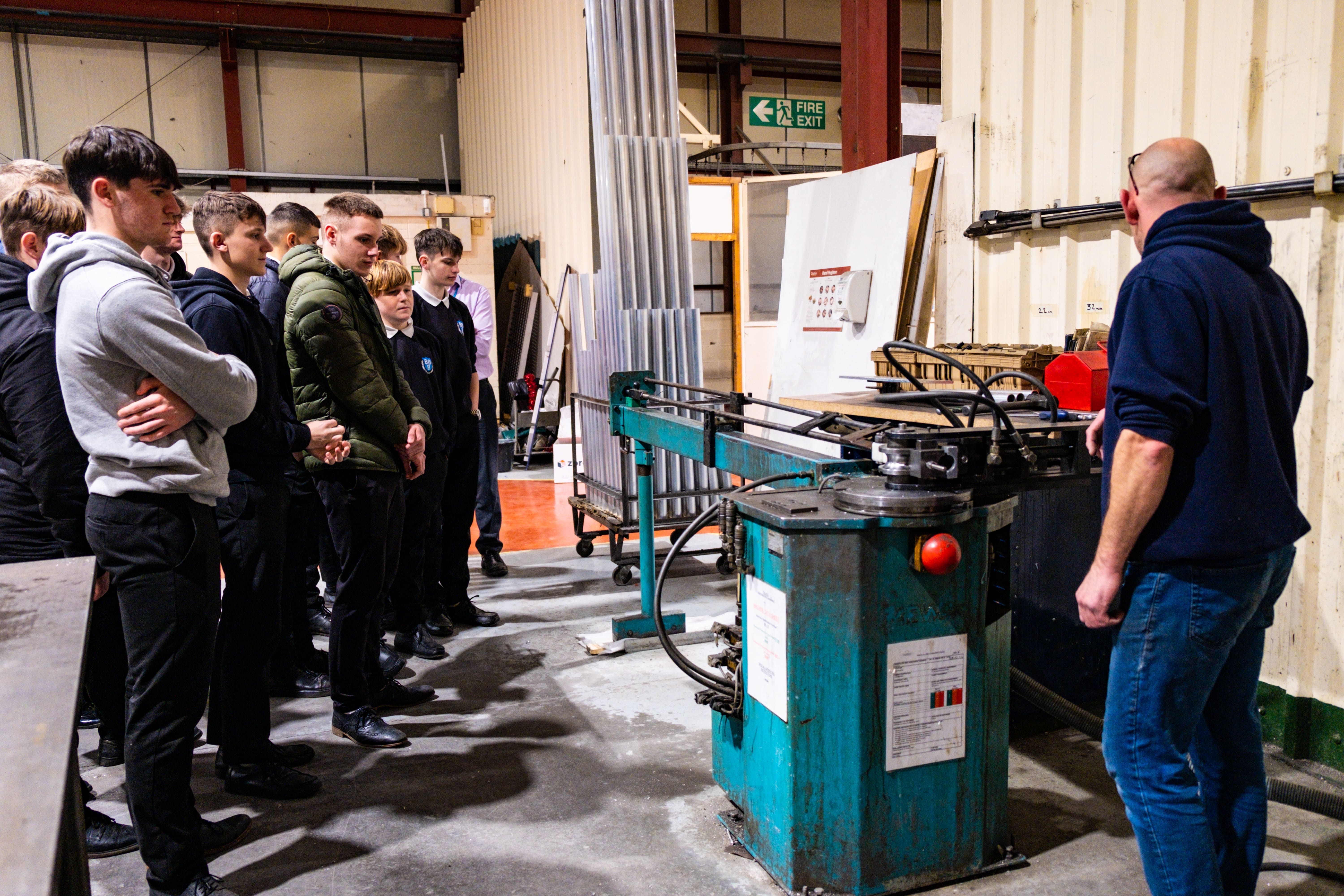
The students were also shown how the tubing is cut precisely to the correct curvature on the Kaltenbach automatic circular saw.

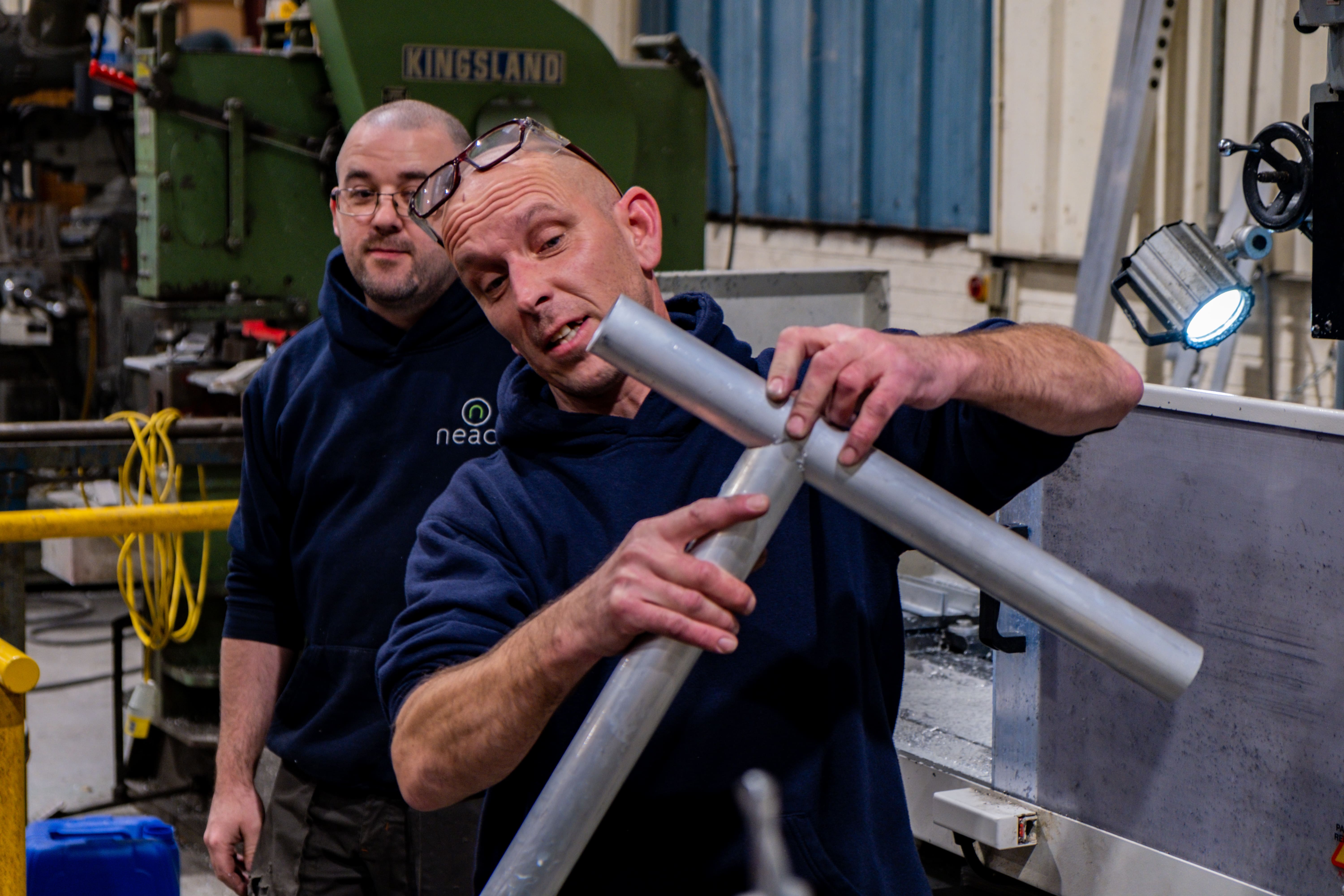
Once the aluminium tubing was ready, the students then got to witness the tubing being coated in Neaco’s nylon and polyester powder coating plants.
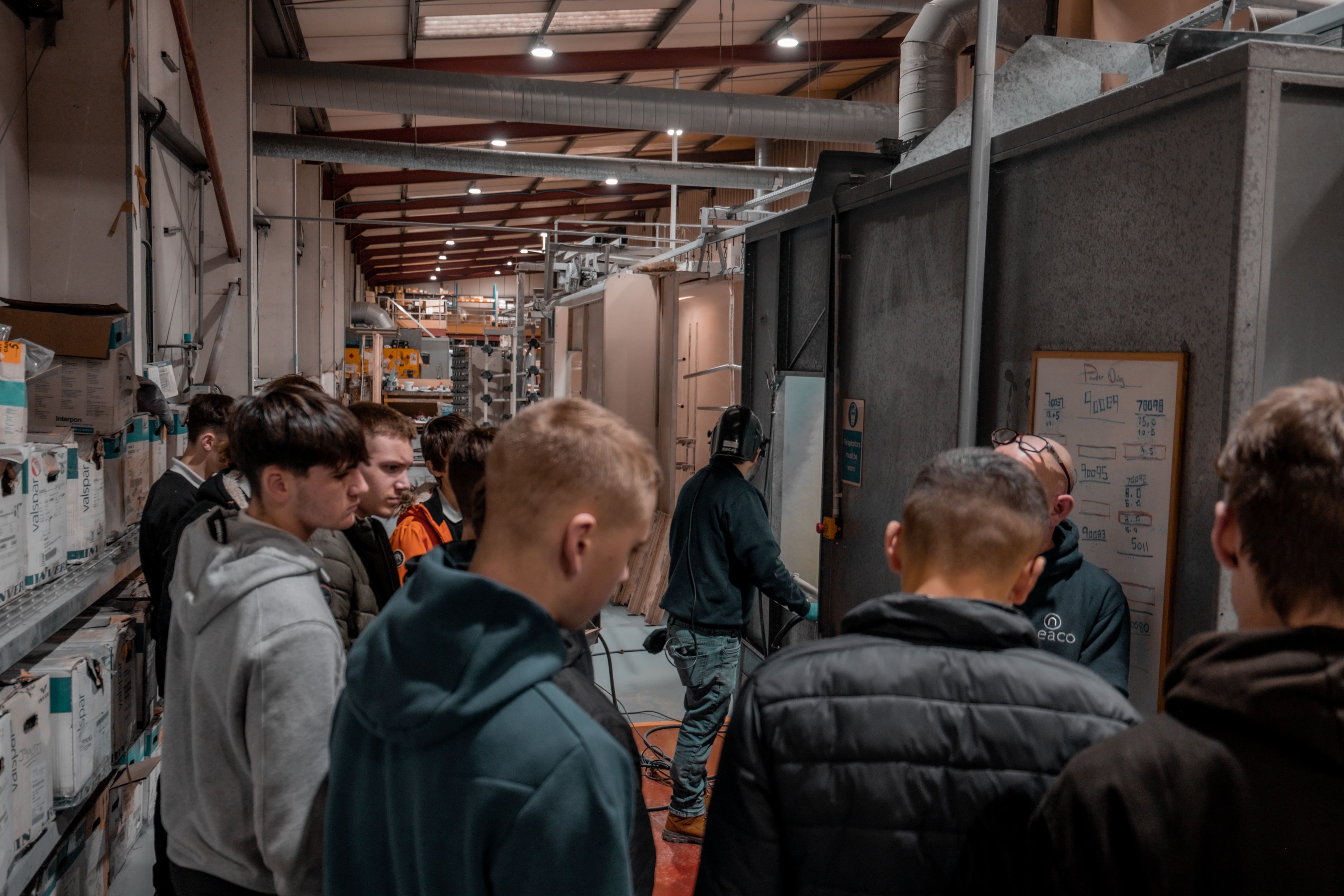
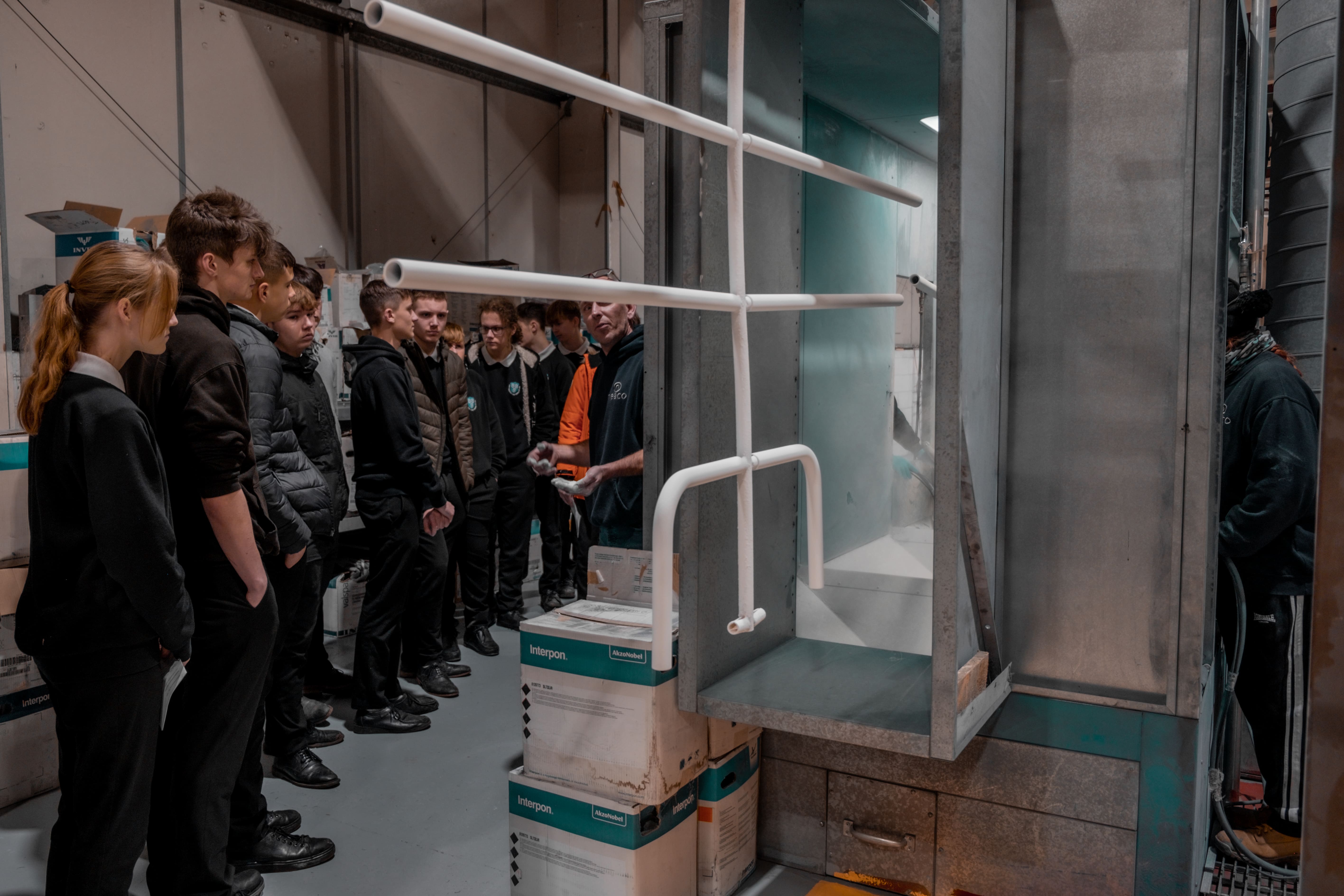
For the finale of their visit, the students visited the CAD department and then received insight from the Sales department. This insight revealed how Neaco proceeds from an enquiry, to technical and then to manufacture. This meant the students received inside information on the whole process and where their engineering careers would fit within a construction company’s product cycle.
The demonstrations were really informative, and the ability for the students to see how raw materials are processed into a finished product range really helped to understand all the theory I teach them in the workshop. I just want to thank you for all the time you gave our students today. It really has made a huge impact on them.”
Mr Andy Grayshan | Head of Engineering and Technology